Matrix - METS Mining Device
Catalyst PDG
Problem
Matrix approached our team at Catalyst to create a new mining device that would track miners as well as provide critical environmental information inside the mine. The device had to be IP-67 to withstand dust and water submersion. It was to be mounted or hung from inside the mine walls using removable brackets. It included a swappable battery pack, LCD screen, and fuse access panel for maintenance.
Solution
We created a rugged, overmolded PC/ABS enclosure for the necessary electronics that fulfilled all functions proposed within our form. It was designed for use with the existing Matrix METS 2.1 System, utilizing wired and wireless communications, electronic tracking with radar and CO monitoring system designed for use in coal mines. The device was designed with flexibility to be compatible with multiple node configurations.
Role:
Lead product design engineer - full assembly owner
Timeline:
6 months

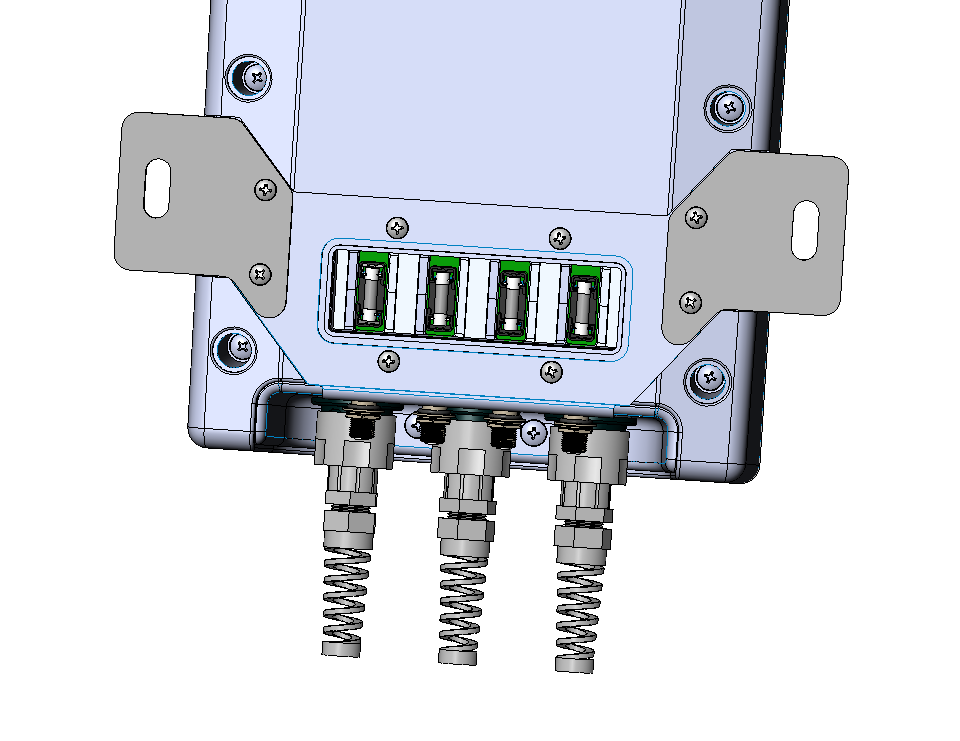
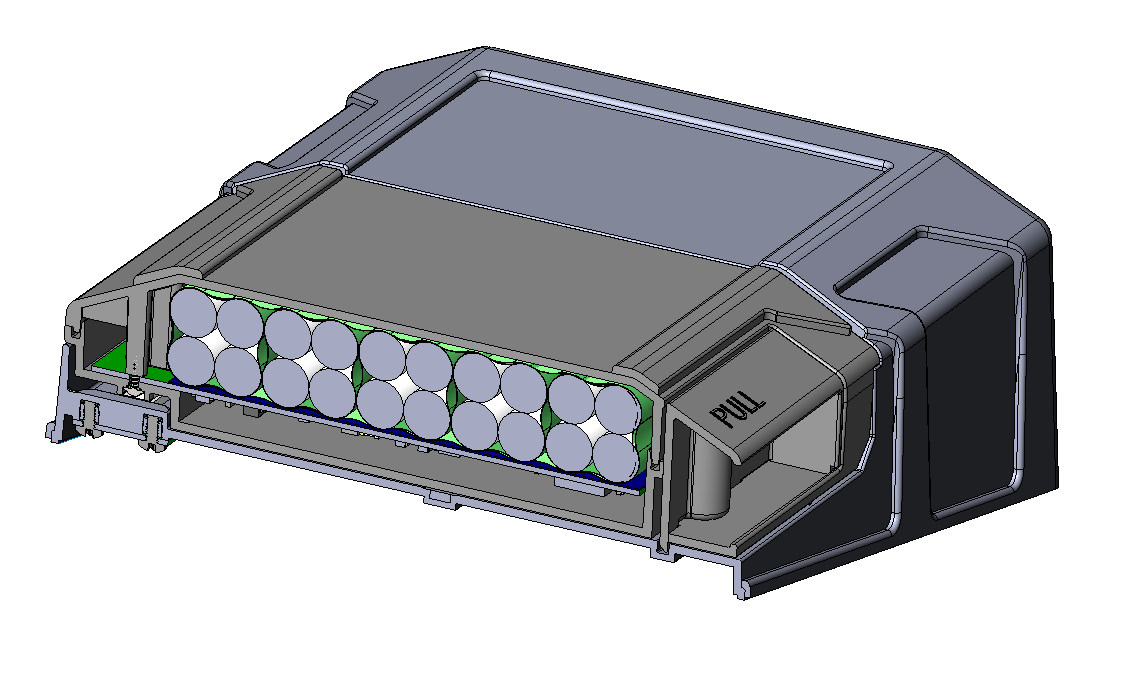
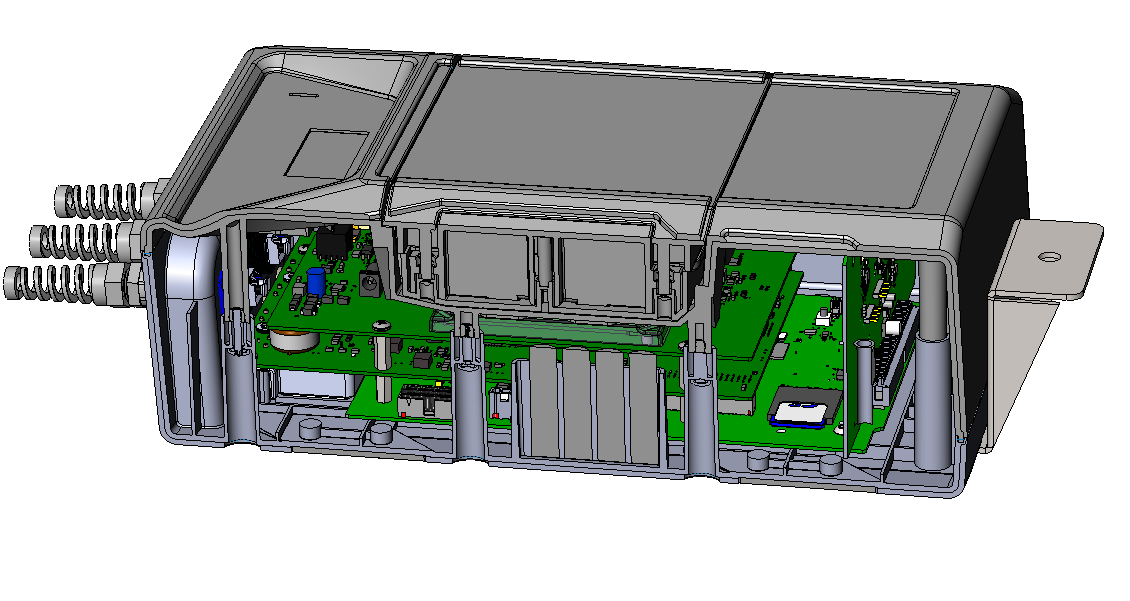
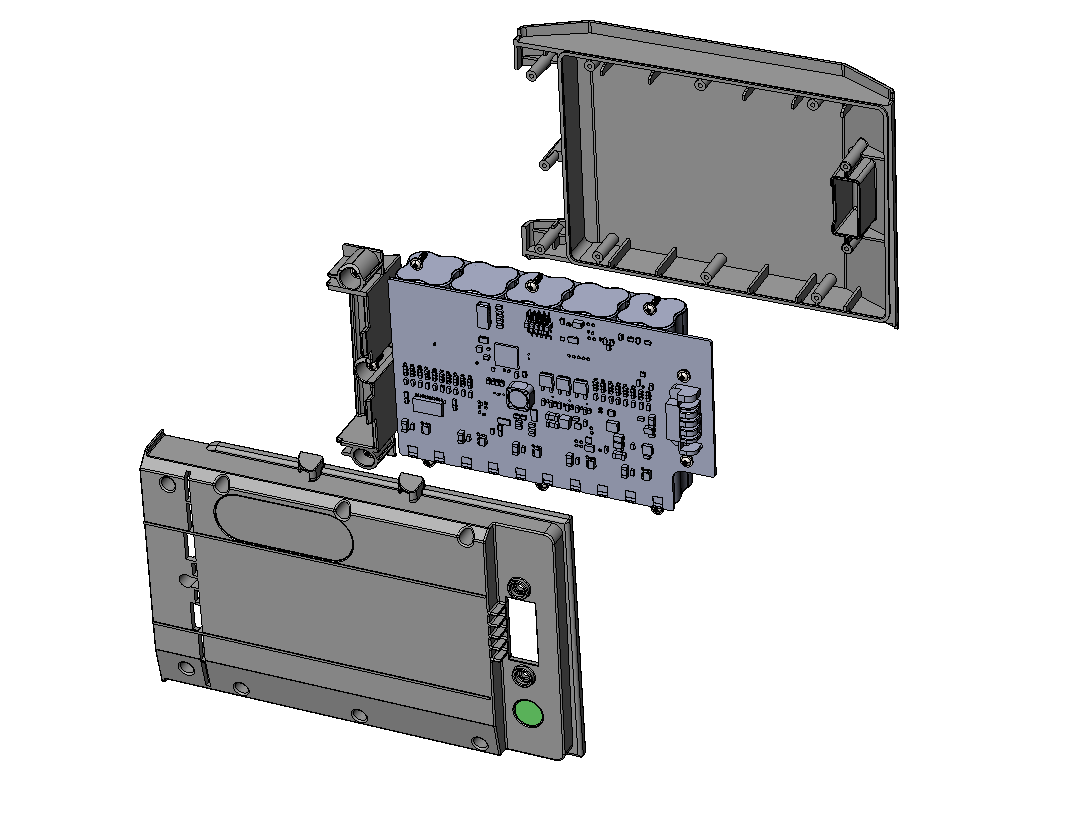
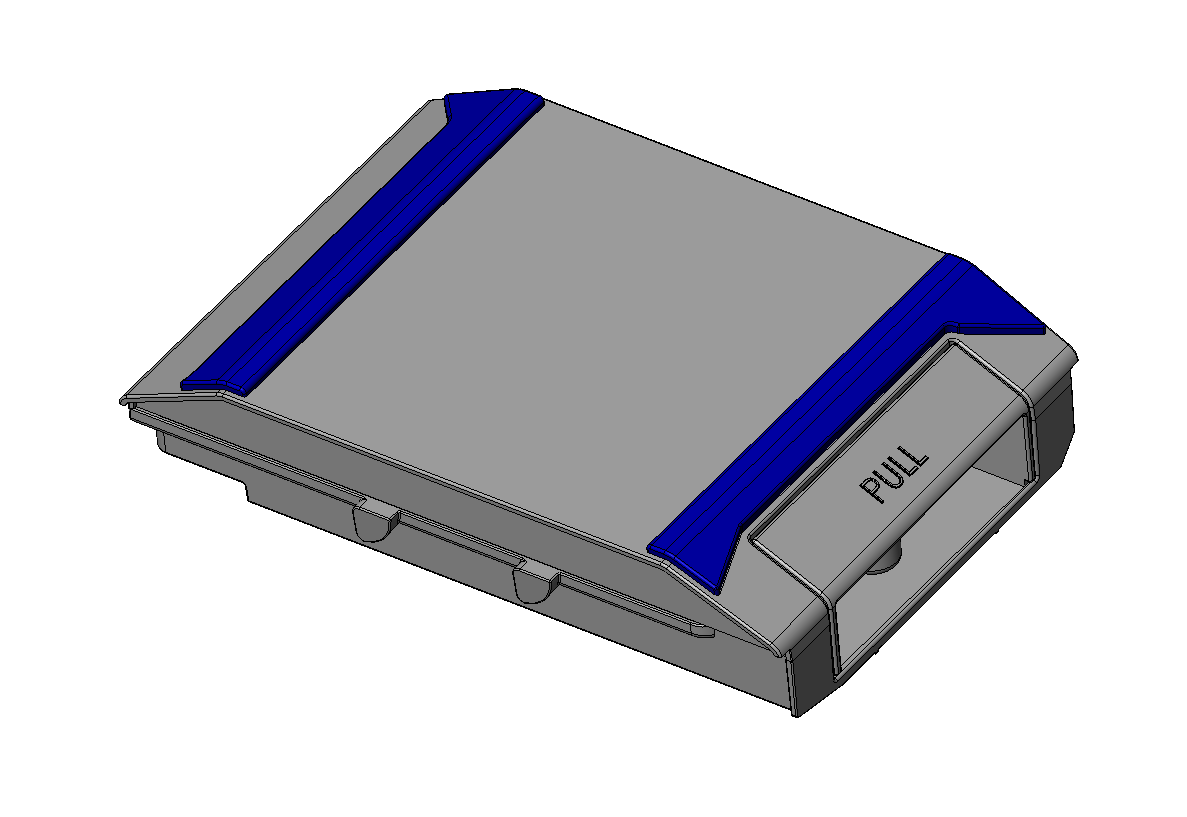


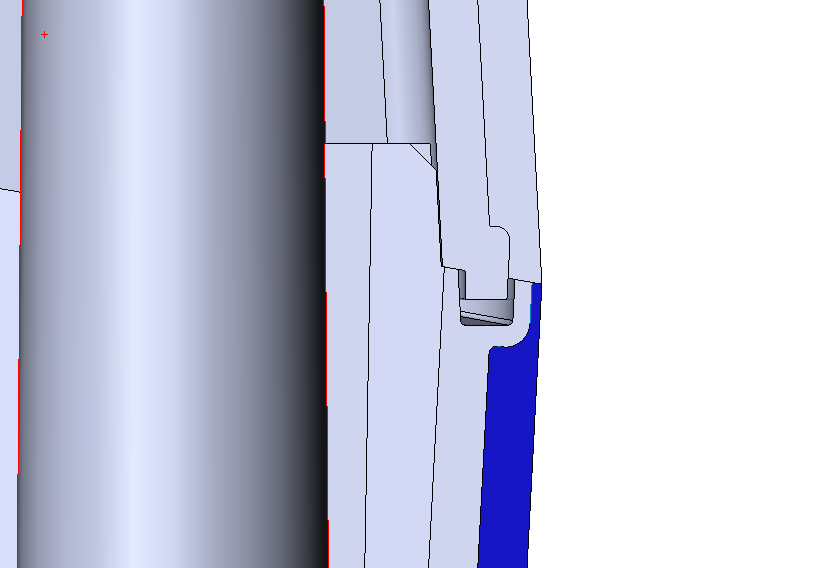
Challenges Met
Waterproofing Seals
This was my first time designing an IP-rated enclosure so I learned alot about designing for those requirements. I designed multiple seals and a diagonal split in the housing with silicone gasket and compressive rib for sealing. A Gore-Tex patch was used to allow ventilation without compromising the IP rating.
Overall Product Size
The size of the housing was driven by the electrical components and orientation required for function. This created challenges including screw boss placement and plastic wall thickness considering draft.
Working With EEs
I worked directly with electrical engineers and radio antenna specialists on specific spacing requirements and material constraints within the housing. PCBs, electrical components and sensors had to be adjusted and spaced accordingly for the stackup to fit within the most minimal thickness possible.
Interchanging of Components
I developed a mechanism to lock in the battery pack, which had to be removable with a pull handle. The fuse box also had to be accessible, which required a separate compartment and sealing door. The mounting plates also had to be removable.
Accident and Drop Protection
The enclosure had to be rugged to withstand any impact in the event of an accident. The overmold for this product was to enhance drop protection but also aesthetic to give it a more rugged look. I had to consider the second TPU shot and draft, wall thickness, and proper shutoff.
Cost and Timeline
This was a complex assembly with many components so cost had to be considered in the design. Like all clients they wanted this done as quickly as possible.
Skills Demonstrated
Master assembly design
PCB integration
Waterproof design
Mechanism design
Overmold design
Plastic part design
Designing with tolerances