Gamblit - Tri-Station
Gamified Slot Machine
Catalyst PDG
Problem
Slot machines typically drive an older audience, and do not get much engagement from the younger generation. Gamblit set out to bring a game-based digital experience to gambling, to go after the 21-35 year old audience, providing an alternative to traditional slot machines.
Solution
We created an integrated touchscreen gambling station with a sheet metal housing enclosure to allow for app-like gambling to be placed in casinos, cruise lines, or bars.
Role:
Product Design Engineer - owner of display frame and armrest areas while supporting other areas of the assembly
Timeline:
9 months
Sketching and Brainstorming
CAD Screenshots




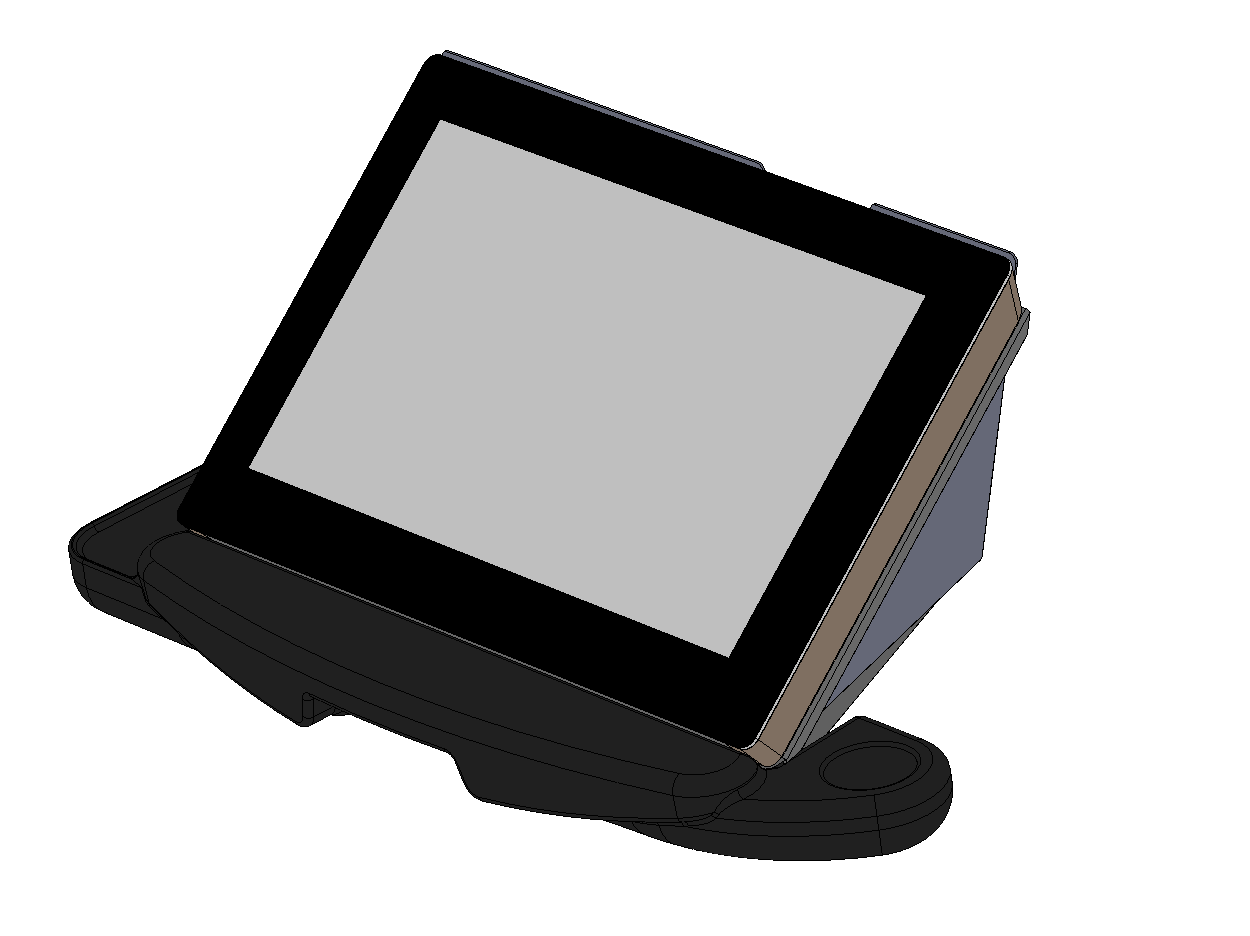

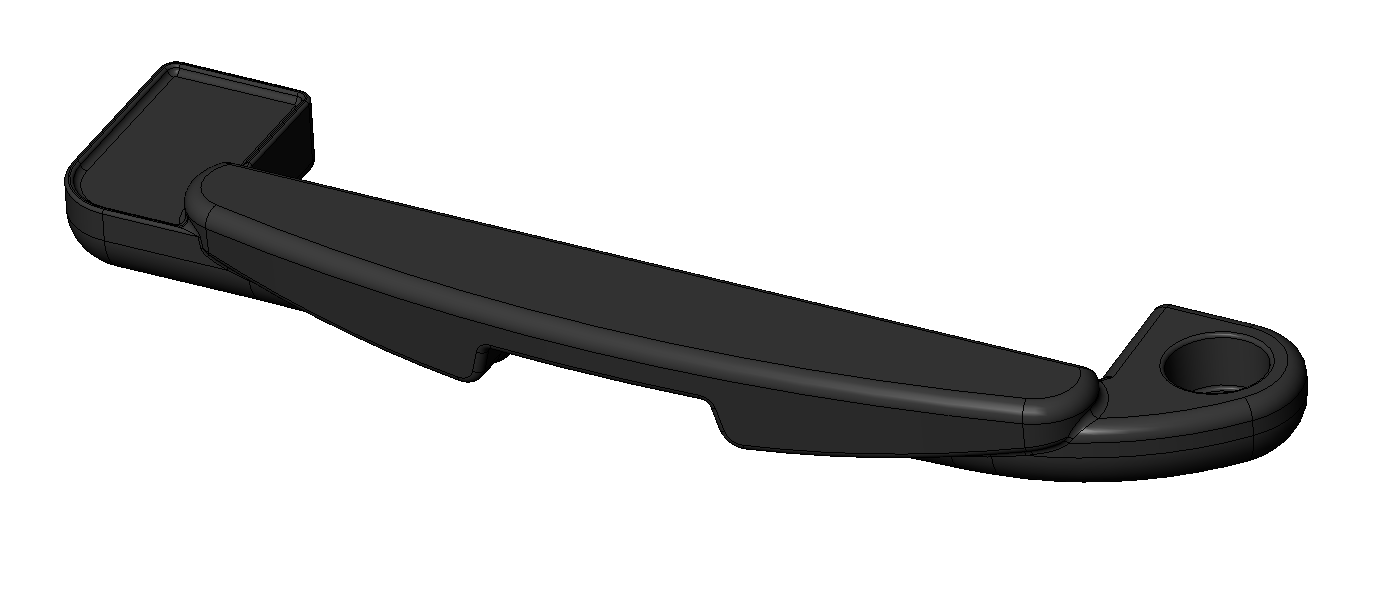

Challenges Met
Changing Interior Parts
Interior components and hardware were sometimes changed causing redesign and moving of components and sub-assemblies to fit.
Heat
We had to design in fans into the enclosure to ensure proper air flow and ventilation of components, which were spaced accordingly.
Use Cases
Many aspects of the uses cases played a part in the design. For Instance we had to consider the weight of a large, potentially drunk human at a casino leaning on the arm rest, as well as where they would want to put their drink and phone down. I used FEA on the display frame to validate the structure.
Screen Sealing
Because the touch-screen display area was a risk for spilled drinks, it had to be sealed off properly to reduce the risk of damage.
Integrating Electronics
The electronics required power, so we had to consider where the cables would live which was particularly challenging on the sliding touch screen which had to be able to slide open for maintenance access.
Timeline
Like many of our projects, the client wanted this right away. However because the assembly was so large with so many components, holding the schedule was always challenging. It was mostly me and another senior mechanical engineer working on it.
Skills Demonstrated
Sharing Large Assembly
The other ME and I checked in and out parts as needed to tag team certain sub-assemblies.
Sheet Metal and Fastener Design
Many sheet metal bends, bolts, welded nuts and threads coming together to build this structure. Many fasteners were used, which we had to make sure we had room to put it together.
Creative Mechanism Design
The display had to be rigid but also slide out of the way for maintenance, using a locking latch mechanism.
LED Light Box Design
The light boxes were designed to be assembled separately and had to be able to disperse the LED light evenly