
Car & Desk Mount
Popsockets
Problem
In a saturated market of car mounts, Popsockets set out to create a mount that was a unique solution to windshield and dash mounting for Popsockets customers. It needed to be within a certain size, price point, and timeline to market.
Solution
The mount, which is now a top selling SKU, hits all requirements by providing an innovative way to view a phone screen from all angles and orientations with each joint allowing full rotation around each axis. It also offers steady support of the device, even while fully extended, in a collapsible form that fit the company’s design language. While it makes a great mount to use in a vehicle, it also doubles as a great desk or surface mount.
Role
Lead Product Design Engineer - Full Assembly Owner
Timeline
1 year from initial concept to mass production


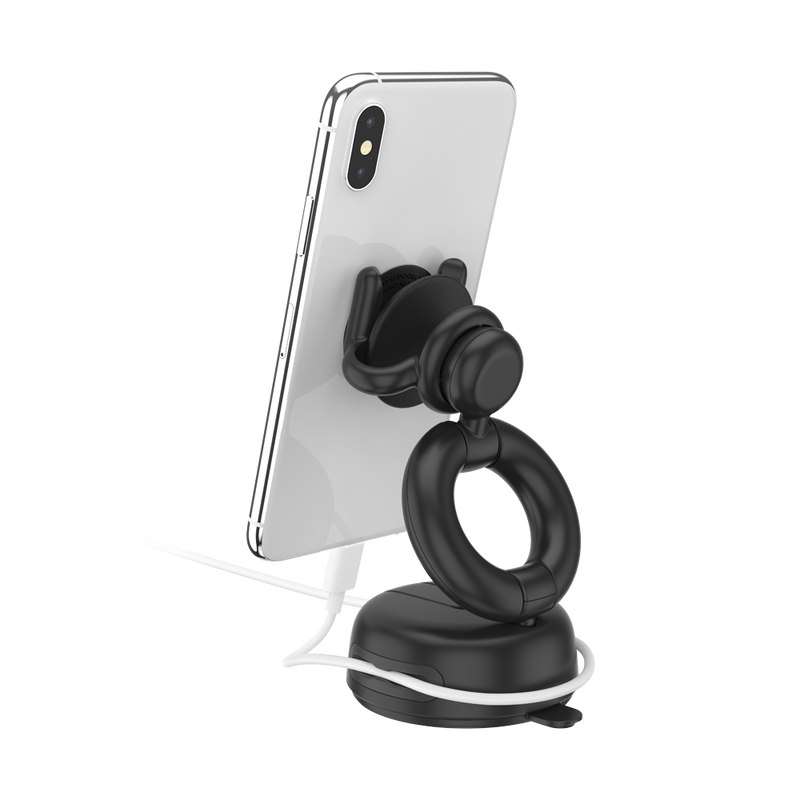


Prototyping
I created various rounds of prototypes with Objet 3D printed, machined, and off-the-shelf parts to test assembly and functionality.
This was critical for overall form and function, but in particular for the lever and suction cup cam mechanism, and the snap fits of each circular section of shell component.
There were multiple size iterations as well as concepts for the friction hinge, requiring constant prototyping and iteration.
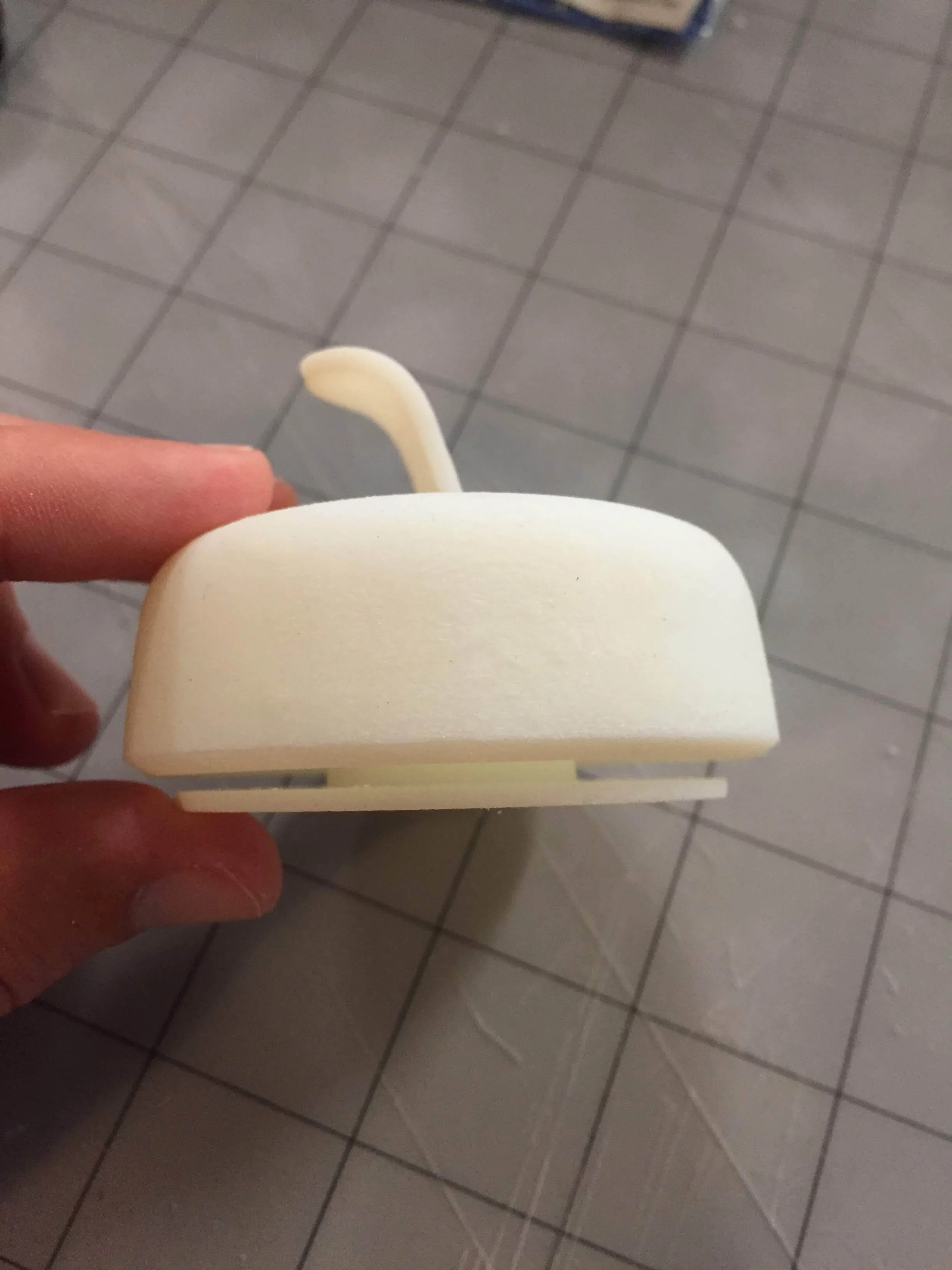



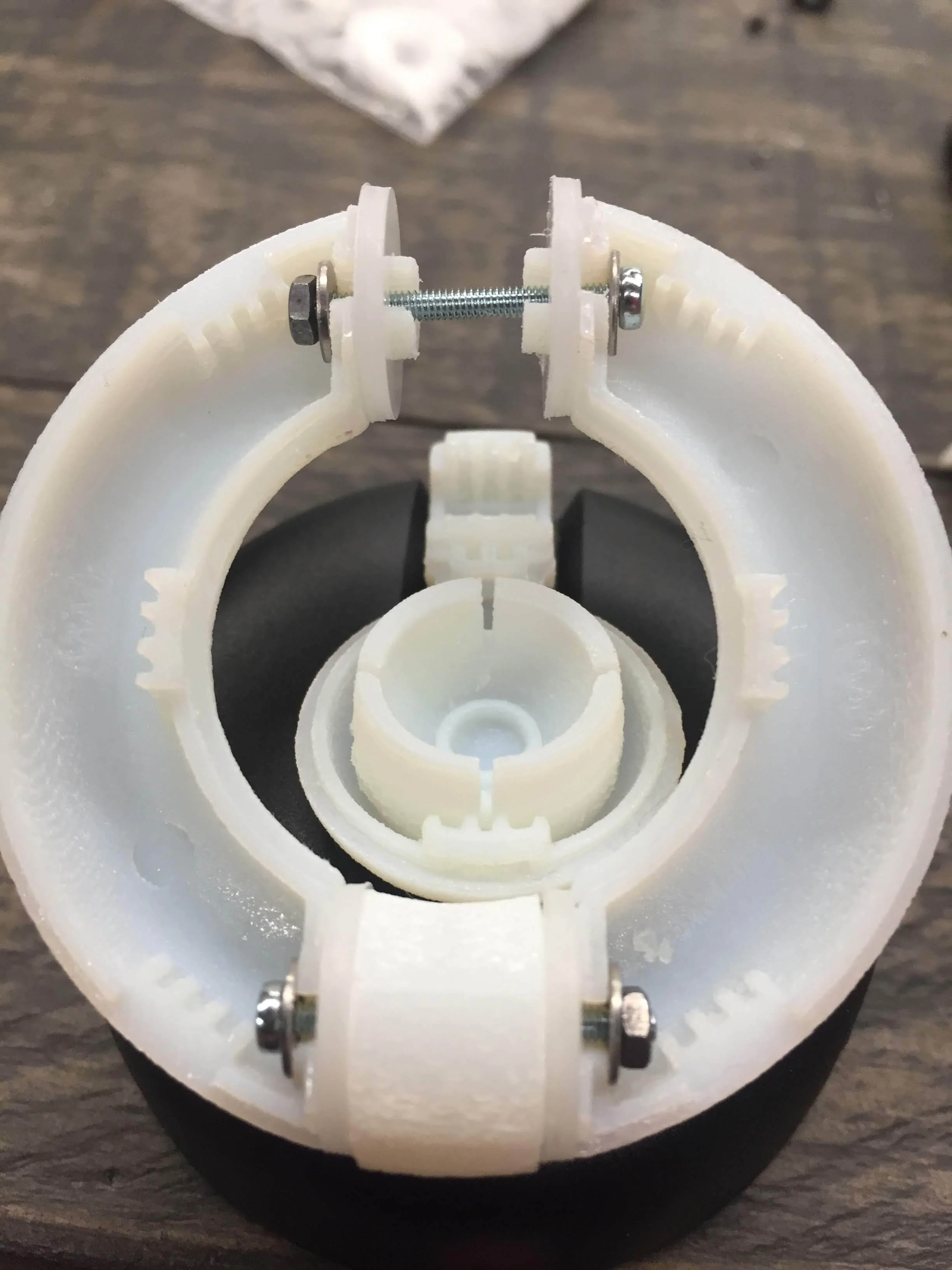
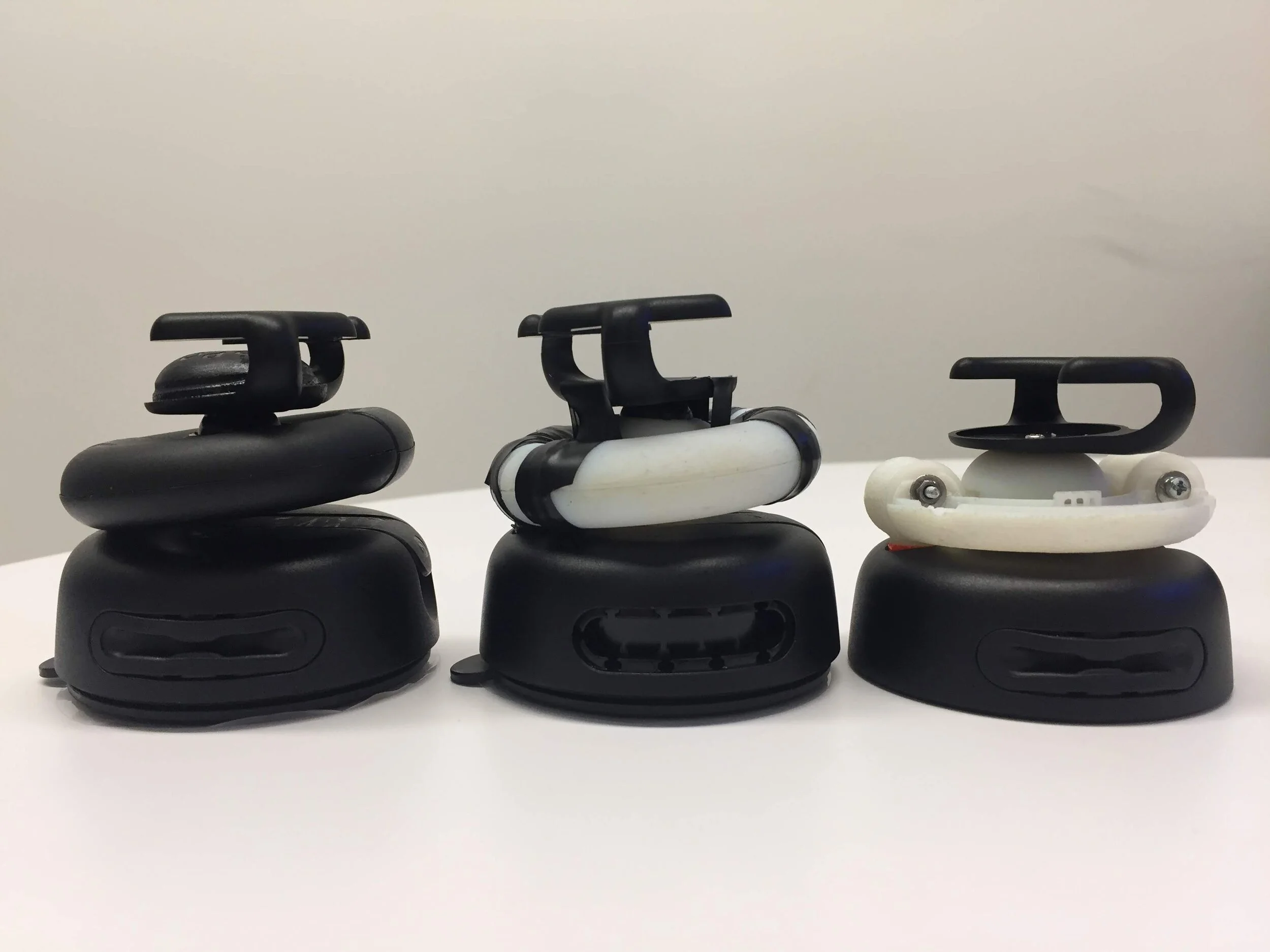
Engineering Development
Challenges Met
Cost
Maintaining a low cost solution for this concept to meet a $30 price point was a challenge that drove multiple iterations. The initial design used TPU “brake pads” to create friction in the hinges. Once this method was determined inadequate in terms of friction, we worked with new suppliers on a custom constant-torque hinge consisting of two pieces of sheet metal wrapped around a simple machined shaft.
Mount Head Variation
Throughout the design process we went through multiple generations of mount heads, which all required design changes. The mount head was an ongoing project in parallel. The earlier design for this mount included a ball joint mechanism which we developed but determined unnecessary and removed to save cost.
Timeline
Speed to market was important for this project which drove an aggressive schedule including multiple rounds of proto tooling and finally production tooling. This required working directly with our CM and multiple trips to China. The project took about one year to get from initial concepts to high volume manufacturing.
Maintaining Aesthetics
As with many Popsockets products within the design language it was a challenge to maintain the curvature and circularity of the form. Minimizing the overall size was critical to promote a portable and collapsible product. By maintaining the overall ID we had to come to a consensus on spacing for mechanical features which limited my options.
Function
When determining mechanical requirements we had to design for the worst case situations. The friction of each joint had to be determined at each orientation from the weight of the largest device on the market in the bumpiest road conditions. The suction cup also had to be strong on various surfaces. This required FEA on components as well as real-life testing in vehicles. I also implemented an add-in plate solution for mounting on heavily textured and curved surfaces.
Assembly
The assembly included many moving components that had to be tight fitting without hindering the movement or creating any unwanted feel or sounds. I performed tolerance stack-ups and many minor tool modifications to tighten the fit while keeping proper clearance. The order and method of assembly was considered throughout the process and optimized for lowest cost.
Skills Demonstrated
Project management
Mechanical aptitude
Master assembly (top-down) design
Detailed plastic and metal part design
Communication with overseas manufacturers
Tight tolerances and gap control
Working with ID
The dash mount has become a top seller and has received great reviews across the board. Overall this was a difficult project but I’m proud of the result and the fact that the mount has found additional use cases such as desk mounting for WFH needs during quarantine.